
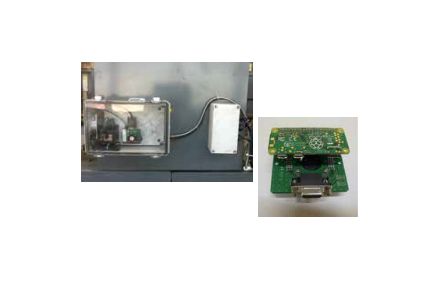
IT・IoT・技術
製造業
IDEC横浜の専門家が伴走支援 工場のIoT化で生産管理体制の改革へ
まずは現場スタッフにヒアリング 情報収集機を自社開発
創業75年。協和合金の事業の柱は、マニュアルトランスミッション車に組み込まれているシンクロナイザー※の製造販売だ。この部品はメーカーや車種により異なり、国内外の自動車メーカーからの様々なオーダーに応えている。
2018年にIDEC横浜が実施した、IoT導入に向けた専門人材育成スクールへの参加を経て、本格的に本社工場のIoT化への取組を開始したのは2020年5月。新型コロナウイルスの感染拡大が始まっていた頃であり、生産性向上の課題が突きつけられていた。
「まず何からやれば良いのか、IoTのノウハウが全くありませんでした。そこでIDEC横浜の相談事業に申し込み、IT・デジタル化の専門家を紹介いただきました」こう話すのは、同社でIoT化を担当する企画部の林氏。月に2回、IDEC横浜が派遣する専門家のアドバイスを受けながら、情報収集機のソフトウェアとハードウェアを自社開発。工場の現場担当者たちに状況をよく確認しつつ、課題解決につながる機能を搭載した。約2年経過し、工場の約100台の設備に情報収集機を取り付け終わった。
※マニュアル車のスムーズなギアチェンジを可能にする部品
収集データを全員で共有 意識と行動にも変化
IoTシステムを導入して、工場内に設置されたモニターで稼働状況をリアルタイムに確認できるようになった。
「稼働時間、生産数は日々確認します。稼働率を自動算出するので、課題や対応への取組が早まりました。数値化されると納得して行動でき、目標感も出てきます。自分達がこれまで気が付かなかったことに気付くきっかけになりました」。
設備の異常停止も一目で把握でき、対応が早まることによりタイムロスが激減した。また、工程ごとの生産性が把握できるので、どの工程に滞留(工程間在庫)があるかがすぐに把握できるようになったという。様々なデータを一元管理・分析し、工場全体の最適化につなげている。「今回の取組は、まだ社内の一部での運用に留まっています。今後は、徐々に会社全体への活動に昇華させていきたいと考えています。効率化によって削減できた費用をより有意義な取組のために充てていきたいです」と取締役の高島眞吾氏は話す。
2023年2月からは、生産工程の出来高を即時に把握でき、IoTシステムの連携を組み込んだ新しい生産管理システムが稼働した。現場の作業者が日報を直接入力するタブレット端末も順次導入予定だ。
(支援事例集2023掲載)
成功のポイント
- 中小企業デジタル化相談事業を活用した自社開発のシステム構築。
- 専任チームの努力と忍耐、そしてIDEC 横浜の技術アドバイザー(デジタル化分野)の的確な指導。
- 会社全体としてのデジタル化への意識の高さと専任チーム・製造現場との連携。
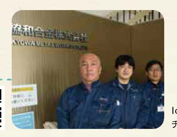