
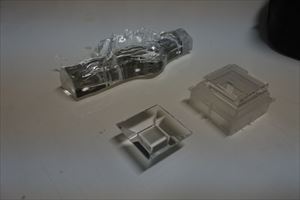
経営改善
製造業
医療分野のコーディネーターのアドバイスによりフェイスシールドを商品化
コロナ対策でマスクなども商品化
電気製品から日用品、自動車…。プラスチックはあらゆる分野に使われ、私たちの生活にも欠かせない素材になっています。プラスチック(樹脂)射出成形を手掛けるロッキー化成(都筑区)は、1981年11月の創業以来、一貫して成形技術の腕を磨いてきました。創業当時は、製造業の国内生産に活気があったことから、同社も電気製品のプラスチック筐体などの量産品をメインにしていました。
ところが、鎌田和明社長が創業者から事業継承したのちの2012年4月、大きな危機に見舞われます。当時、売上の9割以上を占めていた携帯電話関連の仕事がストップしたのです。理由は発注企業の倒産。先が見えないなか、どうするのか…。それでも「元来、プラス思考」という鎌田社長は前に進みます。着手したのは、品質が良くても“安かろう”だった量産品からの脱却。「誰もがやりたくない。やらない分野」(鎌田社長)として目を付けたのが、肉厚(10ミリ以上)なプラスチック部品の成形でした。そして「厚肉成形」という言葉を前面に打ち出し、専用ホームページでもPRしました。
レンズやスイッチなど、同じプラスチック成形品でも、厚さが大きいと製造の各工程に時間や手間がかかります。例えば、乾燥工程一つをとっても、薄いものより、厚い方がはるかに時間を要します。そのため、逆にこの分野をやることで、大きな差別化になるのです。鎌田社長のねらいは的中し、現在は電機メーカーから引き合いがあったカーナビゲーションのスイッチ部品など、付加価値の高い製品づくりへシフトしています。また、人員も拡充し、設計、流動解析なども自社でカバーするようになりました。
フェイスシールド1万枚販売
新型コロナウイルスの感染拡大により、マスク不足に陥っていた2020年5月、同社は、得意のプラスチック成形技術を活用し、マスクとフェイスシールドを開発しました。商品化に当たっては、医療現場のニーズを汲み取れるよう、同分野に詳しいIDEC横浜のコーディネーターがアドバイス。中でもフェイスシールドは、繰り返し使用するフレーム部分に、使用後に除菌シートで拭きやすいような形状を採用しました。こうした甲斐もあり、すでにこのフェイスシールドの販売数は1万枚に達しています。【2021年度支援事例】
成功のポイント
- ものづくりへの探求心を糧として、負の経験にとらわれず、チャレンジし続ける姿勢。
- ニーズを聴き取り、技術の応用と組合せにより、複雑な加工プロセスを構築する力。
- 課題に応じて、複数のIDEC横浜コーディネーターから必要なアドバイスを引き出し、それを受け入れる柔軟性がある。
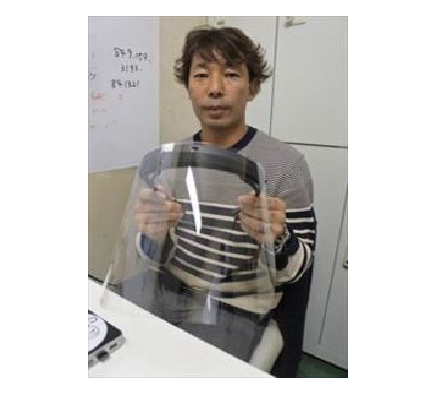