
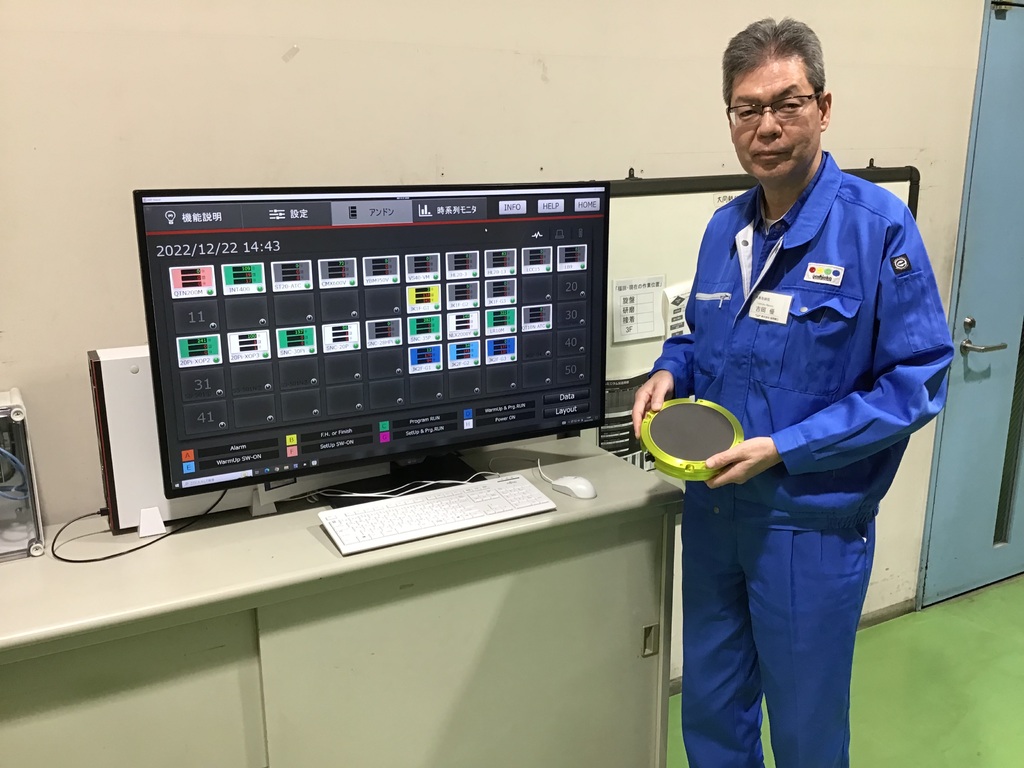
補助金・助成金活用
製造業
グリーンリカバリー設備投資補助金を活用 照明をLEDに変更、コスト削減&脱炭素
水銀灯からLEDへ 実行のタイミングで補助金を知る
吉岡精工は、高い技術力による超精密加工を得意とする。創業は1961年、自動車のエンジンバルブの金型作りで事業をスタートした。各時代のニーズに応えて技術力を磨き、現在では半導体関連事業の割合が増えている。その看板製品の一つが「ポーラスチャック」。フィルムや基板などあらゆる“薄いもの”を加工するための“台”だ。平面に“薄いもの”を高精度で吸着固定させることにより、変形することなく加工することができる。
2022年9月、同社は工場に設置していた水銀灯を全てLEDに取り替えた。
「入れ替える時期が来ていたため、あらかじめコスト計算はしていました。LEDを入れ替えた場合、購入コストと電気料金との比較で3年後に採算が取れる試算でした」と常務取締役の加藤誠司氏。このタイミングで知ったのが、グリーンリカバリー設備投資補助金だった。
「IDEC横浜からのメールマガジンで補助金の存在を知り、すぐに確認して書類を揃え、申請しました」。
コスト削減は 売り上げアップと同価値
工場内の照明をLEDに入れ替えてすぐに実感したのは、隅々まで「明るい」ということ。計測したところ、以前と比べて平均で約4倍の明るさとなった。図面も見やすくなり、精度を追求する現場の仕事にとって重要な環境が整ったことになる。では、コスト面ではどうなったか。
「LEDに交換後、前年の同じ9月と使用電力量を比較して、12%削減になりました」と加藤氏。折しも、電気料金の値上がりに見舞われている昨今。コスト増は避けられないが、LED効果で値上がり分を丸々被らずに済んでいる。
同社の電気料金削減への取組は、実はその前年から実行されている。工場のIoT化を進め様々なデータが収集できるようになると、気付いたことがあった。一例として、始業時刻は8時だが実始動時刻は9時の日があった。待機電力によるロスを減らすため、原因と思われる朝礼のやり方や重要事項の伝達方法を変えた。社員皆にその理由を説明し、とにかく1か月やってみた結果、電力使用量13%、電気料金約8万円を削減。1年間で約100万円のコスト減となり、ボーナスアップにつながった。今後も、日々の小さな改善をIoTで見える化して共有していきたい。そのためのシステム運用をIDEC横浜に相談していきたいとのことだ。
(支援事例集2023掲載)
成功のポイント
- IoTを活用した省エネは、1か月と取組可能な期間を決めて実施し検証した。
- 文字通り見える化により具体的な成果が出ることで、行動にも変化を及ぼし、社員の取組へのモチベーションアップにもつながった。
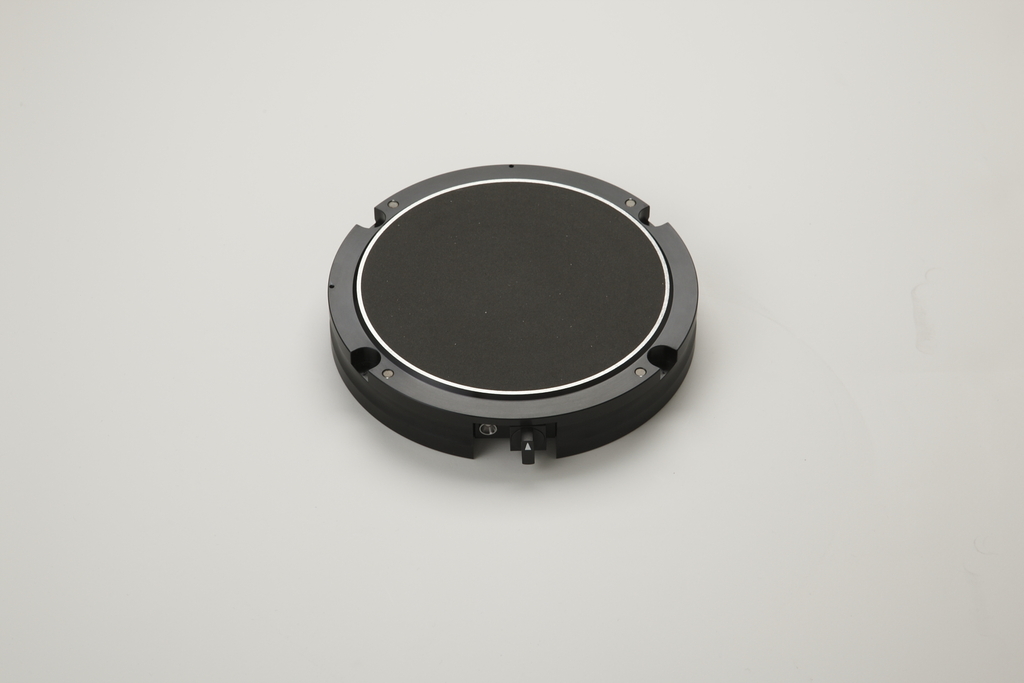